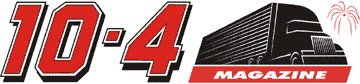
MARCH 2005 TRUCKER TALK
ON THE HOOK
By Writers and Owner
Operators Rod & Kim Grimm

Even with the best preventative
maintenance program, you can’t always prevent everything. And no matter
how hard you try to avoid it, sometimes your truck will end up on a hook.
We found this out the hard way just a few weeks ago at 1:30 AM on a cold
Tuesday morning.
I woke up to an awful
noise – the engine was missing and smoke was pouring out of the stacks.
Rod babied it down the hill to the Pilot in Carlin, Nevada. Getting parked
and shutting it off, there was a minute of engine run on. At only 20 degrees,
it would have got pretty chilly had we not had our Rig Master. It was
a really good time to have a generator that’s not tied into the big engine.
So we took a nap and waited until morning when we could call for some
help.
Our first call was to
Kevin at Altorfer CAT in Cedar Rapids, Iowa. After describing what had
happened, he told us it sounded like a cracked injector or a broken injector
tip. He said NOT to start the engine because if the tip was only cracked
this could cause it to break. We ran our first set of injectors to 1,200,000
miles with no problems. When we finally replaced them, we put in six new
(not remanufactured) injectors. There was only 200,000 miles on these
and two weeks of warranty left.
Calling Lostra Bros.
Towing in Elko, Nevada, we thought we’d only need to be towed to Elko.
They got a truck out right way. They were very helpful getting the number
for Kenworth after we found out that Cashman CAT couldn’t look at it for
two weeks. Kenworth said that they wouldn’t be able to look at it until
at least Friday. Our next call was to Wheeler CAT in Salt Lake City, Utah.
They could look at it that same afternoon if we could get it there.
Our tow driver John
Culver called to make sure it was okay to go to Salt Lake City. He also
asked what the difference in price of just towing the truck and in towing
the truck and trailer would be. For only $300 more, he’d tow both to Salt
Lake. He was very thorough hooking up the truck, carefully running the
power lines and dropping the driveshaft. Rod helped him carry the driveshaft
up to his truck. John told us, “You’d be surprised how many drivers won’t
help.”
There
wasn’t enough room in the tow truck for Lizzie and Starbuck (our dogs),
so with the generator running to keep the truck warm, they had to ride
in the back. Stopping at the Port of Entry in Utah, I checked on them,
and then made us each a sandwich, then we were on our way again. Along
the way, we learned a lot. John, who told us he’d been to special classes
for tow operators, was very knowledgeable. “On a short tow, maybe 10 or
less miles, you can get by not dropping the driveshaft. But if you have
an automatic transmission, there is NO distance you can be towed without
dropping the driveshaft,” said John.
Being towed isn’t ever
cheap. For us, our bill came to almost $1,400 to have our truck and loaded
trailer towed 250 miles. But before you complain about the price, think
about everything involved. The investment in the equipment for the job
can be pretty staggering, as well as the liability of the job and the
knowledge of the driver. Personally, I want them to have good equipment
and know how to use it. Our entire world (truck, trailer, load and dogs)
was hanging from that hook.
Had the warranty on
the injectors covered towing, we’d have had to go to Twin Falls, Idaho,
because that is where the closest shop was located – but that would have
been way out of our way. If your warranty has towing included, know that
it doesn’t mean you can choose the shop you want to go to. We had a Plan
B set up in case the tip had broken and the truck would be down for days.
Our Kenworth dealer back home had a rental W900 on hold and waiting for
us in Salt Lake City if we ended up needing it. Once we arrived at the
shop, the service manager needed the record of the injectors, which Kevin
(at Altorfer) faxed to him. In the waiting room upstairs they brought
us good news – the tip was only cracked and could be replaced and we’d
be on our way soon. We try to take care of the truck so something like
this doesn’t happen. I’ve said for years that we carry along nearly enough
stuff to rebuild the truck if we had to.
Being owner-operators,
it’s good to carry spare parts. Sometimes, having extra parts can save
you a lot of time and money. Instead of waiting for a shop, you can give
your truck a quick fix and keep on rolling. In our two four-foot-long
boxes between the spread axles of our trailer, we have a spare alternator
(with the pulley already mounted), a set of belts, leveling valve (ours
fits truck or trailer), air governor, air to air boot and clamps, radiator
hose clamps, compression fitting to fix air lines, extra lights, wire,
connectors and spare fuses. It seems like a lot of stuff to carry, but
if and when we ever need one of these things, we’ll be glad we have it.
Rod and our friend Rich Klink recently had to change out the connector
box on the back of the truck one night in Alameda, California. We were
glad that we had the proper parts and tools to get the job done ourselves
and get back on the road with a minimal delay. Rule of thumb: carry this
stuff for years and never use it – leave it home for a week and you’ll
need it. So never leave it at home!
After getting our truck’s
injector fixed in Salt Lake City, we were back on the road and on our
way. All told, we were pretty lucky – our friends Wendell and Lynda Foss
were not so lucky. About a week after our ordeal, they had a breakdown
experience of their own, but it did not go so smooth. Just east of Des
Moines on a Saturday morning, they thought their clutch went out. The
tow experience was fine. I learned from them that it is illegal in the
state of Iowa to tow a truck and trailer together. Tow truck drivers can
only haul a combination to the safest place to drop the trailer.
Making calls to shops,
they found that Kenworth could look at it on Monday, Freightliner could
look at it on Sunday and Peterbilt could look at it as soon as they got
there. They opted to take it to Peterbilt of Des Moines, which they soon
came to regret. By noon on Saturday, when Peterbilt closed, they thought
the center of the clutch had broken. After setting up another truck to
deliver their load, they then went to Cedar Falls to visit with Wendell’s
family for the rest of the weekend.
On Monday, they were
told that the input shaft had broken, but it was a strange break. Road
shock usually causes a jagged break, but this was a clean break. This
was fixed and then more problems were found. Next, they were told that
there was a funny noise in the transmission, and that they (the mechanics)
should look at it. After checking the transmission, they found nothing
wrong (but did still charge them a fee for checking it).
On Tuesday they found
out that they needed a driveshaft because the slip joint had locked up.
Good news – this is under warranty. Bad news – Peterbilt tells them Spicer
is saying the driveshaft is an odd length and it’ll take 10 weeks to get
one. Wendell and Lynda’s truck is a 270-inch wheelbase – how odd is that?
Peterbilt e-mailed Spicer and told them that the truck was broken down
and in the shop and that they couldn’t wait that long. Spicer replied
by saying that it would be 48 to 72 hours for shipping after they found
or built one.
Wednesday’s news: the
truck will be done on Friday. The guys at the shop tell Wendell and Lynda
that the truck will be ready and that it’s okay to load their trailer
for the next load going to California. You can probably guess what happens
next. They arrived on Friday to pickup their truck only to find out that
the driveshaft hadn’t come yet, but it should be there the next morning.
Saturday morning rolled around and still no driveshaft. They waited around
until almost noon before finally renting a truck and heading off to California.
On Monday morning, they
were told that the driveshaft had been mistakenly delivered to Freightliner
on Saturday. Had someone bothered to call and get a tracking number on
Friday or Saturday, this mistake (and subsequent truck rental) could have
been avoided. When Wendell and Lynda got back to Des Moines on Thursday
afternoon, they were presented with a bill that simply had a list of parts
and a total of the labor charges (with no specific breakdowns). The man
at the shop said Peterbilt would be in touch with regards about what might
be covered under warranty and then turned around and walked away. I saw
the bill they were given and we’ve never received anything like it before.
It should show each part of the job individually, including a parts and
labor breakdown, and then a grand total for everything. We felt so bad
for them – what a nightmare their breakdown was!
When you breakdown out
on the road, you are at the mercy of the shop you end up in. As drivers,
we can help one another by telling each other which shops do good work
and provide excellent customer service, and which do not. We have three
places we try to get our work done if at all possible: Kenworth of Cedar
Rapids, Iowa; Altorfer CAT in Cedar Rapids, Iowa; and Bosselman’s in Grand
Island, Nebraska. These places all know us and they know our truck. We
trust these shops, and, in the end, that’s half the battle.
There’s nothing worse
than breaking down – especially when under a load. In addition to towing,
other costs can include hotel rooms, meals, rental cars and lost loads
– not to mention the actual cost of the repair. Bottom line: do everything
you can to avoid a breakdown, but remember, sometimes you just can’t avoid
the hook.
Copyright
© 2005 10-4 Magazine and Tenfourmagazine.com
PO Box 7377 Huntington Beach, CA, 92615 tel. (714) 378-9990 fax
(714) 962-8506 |